Cyclist
Meet the maker: Dominik Dominiak of Project D
For Dominik Dominiak, comfort is king when it comes to bikes. While most framebuilders are looking for ways to reduce weight and increase speed, Dominiak claims that all his efforts are focussed on making the ride as comfortable as possible.
This quest has led him down some interesting avenues with his brand, Project D. The bike he showed at Bespoked 2023 was essentially the result of asking just how far frame flexibility could be pushed without sacrificing stiffness where it’s needed. And with no pesky UCI regulations hampering creativity, he was free to innovate, earning himself not one but two awards in the process.
This fixation on comfort is unsurprising when you consider where Dominiak does most of his riding. A Polish native, he lives slap-bang in the middle of the country in a city called Łódź. His local country lanes are lumpy, bumpy and often completely unpaved – a far cry from the silky-smooth tarmac your average carbon superbike is geared up for.
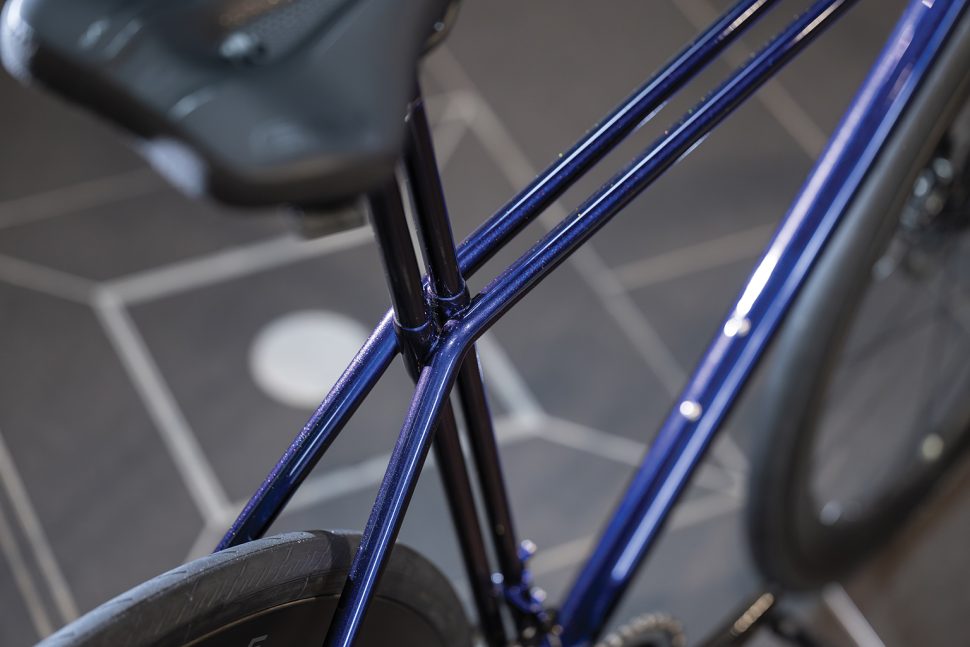
‘I’ve been mountain biking most of my youth,’ says Dominiak. ‘Now I’ve moved to the western part of town, and it’s mostly what people these days like to call “gravel”. But that’s just what our Polish country roads are like. It’s all gravel so you need big tyres and low pressures – you need comfort.’
A lifelong cycling fanatic, Dominiak has been tinkering with bikes since his youth. Over the decades, this has evolved from designing custom stickers for his childhood bicycles to making his first forays into frame design, but it was always his dream to create his own bike brand.
‘I eventually met a guy from a Polish aircraft factory who could weld aluminium. He had his own downhill brand on the side. I asked him if he could build something for me if I gave him a design, and he said yeah, sure. I did the design with a pen and pencil. It was terrible. That’s when I realised I needed to learn CAD [computer-aided design]. It took me about a year, then the second one we built was actually quite good!
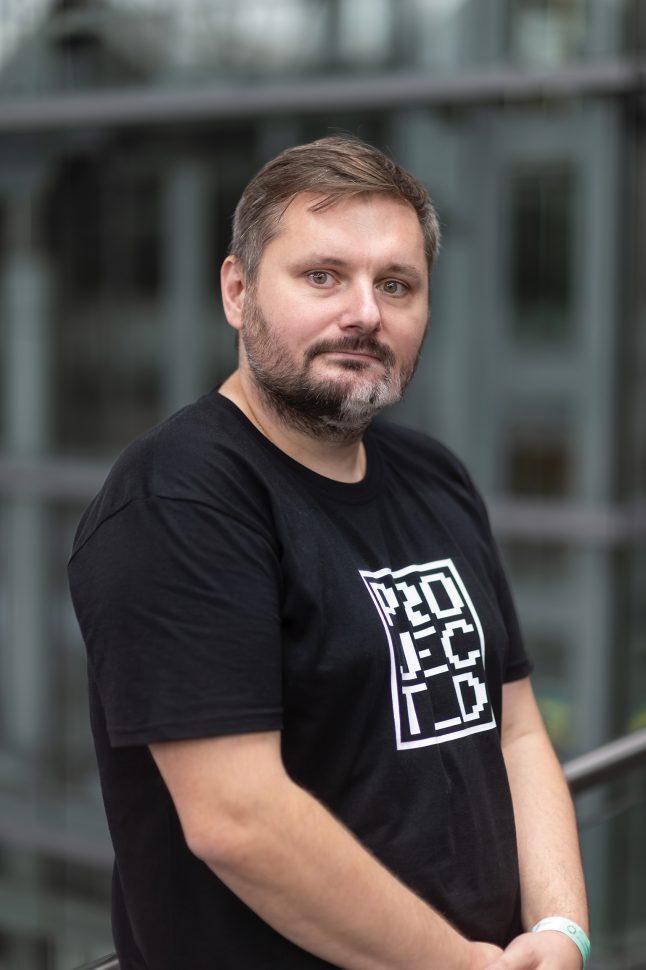
‘It was only around five or six years ago that I felt confident enough to start building with my own two hands. I don’t know what it is – I suppose sometimes you just need a few years to grow. It’s not that hard, and I always had it in me, but I guess you just have to graduate to a certain level to be ready.’
These days, alongside his full-time job in environmental engineering, Dominiak is finally living his dream of owning and operating a bike brand. Everything is done out of his home, and he regularly works on commissions for customers as well as pushing boundaries with his more experimental frame designs.
Double drop
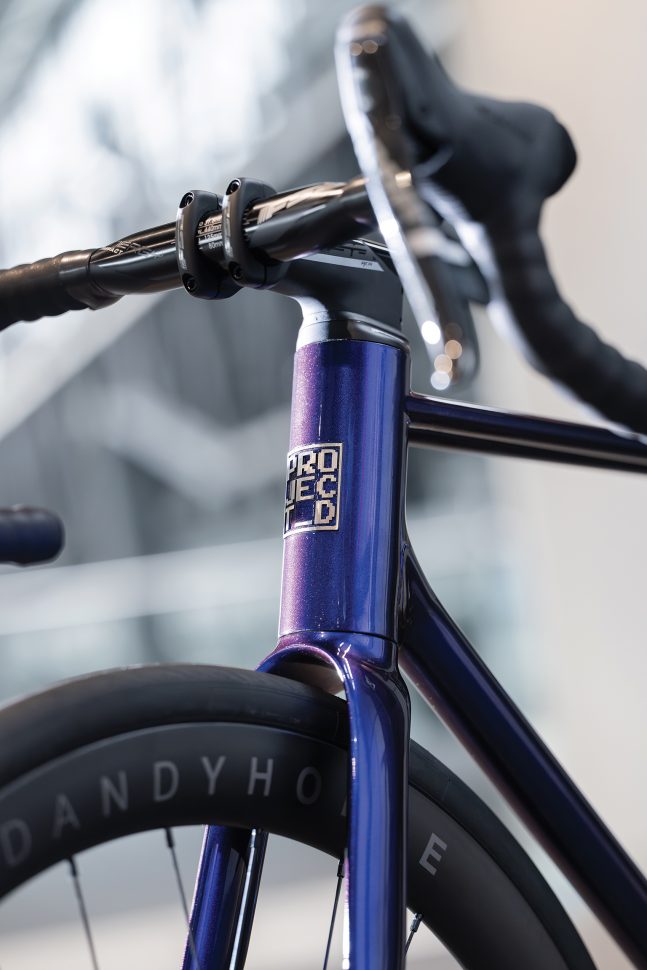
One example is this aforementioned multi award-winning machine, which as yet remains nameless. While looking for a way to maximise comfort in a drop-bar bike, Dominiak started fooling around with CAD, ran some simulations and came to a rather unconventional conclusion: perhaps in some cases, two tubes are better than one.
‘First I decided to split the top tube into two,’ he explains. ‘That way I could have more vertical movement of the head tube without the frame twisting or feeling too noodly when cornering. Meanwhile, the twin seat tubes allow for a bit of sideways twist and back-and-forth swing, all of which increases comfort. And the chainstays are completely 3D printed. They change profile along the length. Kind of like an ellipsis that travels around the middle, like DNA. But it’s not just to look cool – the intention was to add flexibility, and it worked like a dream.’
Another interesting design touch that isn’t immediately apparent is the choice of materials. The frame is actually a steel-carbon split. The down tube is Columbus XCr, and the head tube, chainstays and dropouts are 3D printed 17-4 stainless steel. But the top tubes, seat tubes and seatposts are all made with carbon fibre tubing.
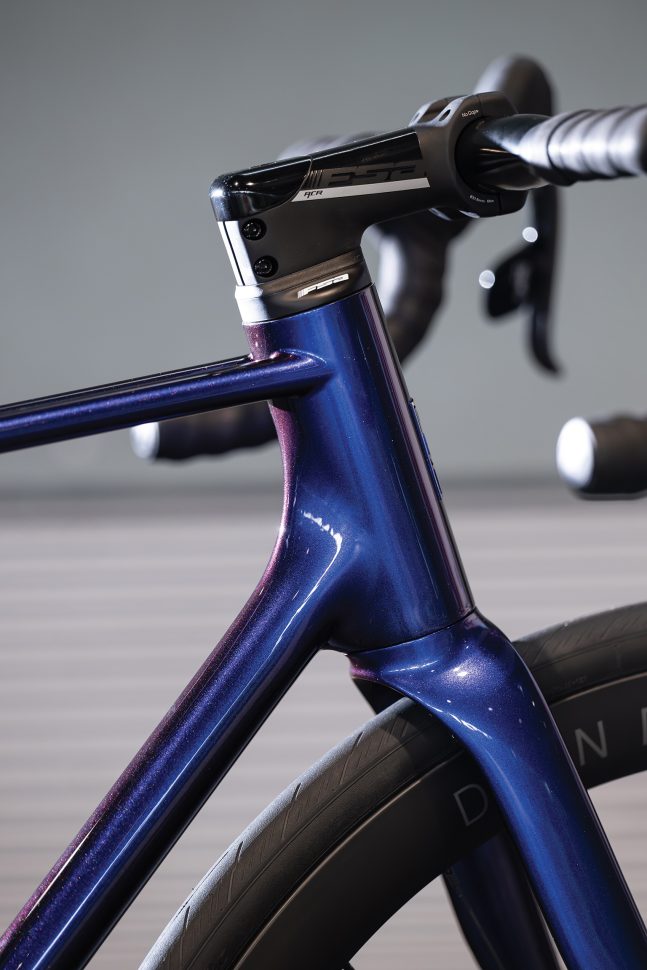
‘What I love about carbon is that you can tailor it by changing wall thicknesses and diameters. So you can actually make it very comfortable, particularly for dealing with low-frequency vibrations. Unfortunately it’s not great for dealing with jarring high-frequency vibrations from the road, so I had the idea of making the bottom of the bike from steel to deal with these, while making the top of the frame from carbon to handle the low-frequency stuff.
‘Mixing materials has always been part of my company,’ he adds. ‘I work a lot with aluminium for 3D printing too, so I think I will always have at least two materials in my builds, sometimes three.’
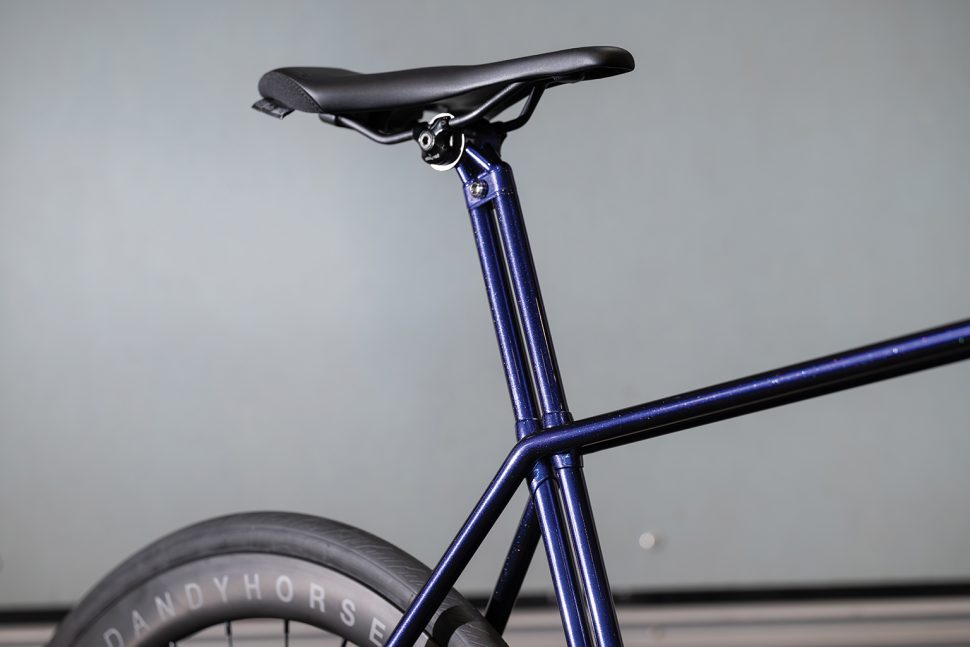
Frame design aside, Dominiak is a staunch mechanical advocate, arguing that electronic shifting robs bikes of their elegance. For this reason he chose to spec the build with a Sram Force mechanical groupset. He also selected a wheelset from Dandy Horse – a Polish brand based in Warsaw whose owners have invested in their own moulds to produce their carbon fibre rims in-house.
Dominiak is taking commissions with Project D, and prices vary depending on the project. That said, if you were after this particular frameset you could expect to spend €5,500 (approx £4,700) excluding tax, which includes the frame, fork, headset bearings and all the gear for the rather special twin seatpost.
‘It’s an extended frameset, let’s put it that way,’ says Dominiak.
See @project_d_bicycles on Instagram for more details
• This article originally appeared in issue 153 of Cyclist magazine. Click here to subscribe
The post Meet the maker: Dominik Dominiak of Project D appeared first on Cyclist.