Cyclist
Inside Giant’s Taiwan factory
Anyone who has spent time in the world of bikes is likely to have encountered someone who says, ‘But it’s made by Giant.’ It’s not meant as a compliment, always as a slight, whether it’s about a Giant bike or a bike they presume is made by Giant. The implication is that something mass produced in the Far East must be cheap and of low quality compared to, say, a bike produced in Italy by a traditional marque.
While perceptions are slowly shifting, this illusory truth still persists today: anything crafted in the West is synonymous with bespoke excellence, while products from Asia are relegated to the realm of budget and mediocrity.
However, a tour around Giant’s carbon production facility in Taiwan – one of a number of factories the company has around the world – would convince even the most hardened cynic that Giant’s top-end road bikes are at the cutting edge in terms of technology, and produced with a care and quality that would make any artisan framebuilder proud.
On another level
Giant’s Taiwanese facility truly is giant, and the outside of the building is fronted by a fittingly giant Giant sign.
‘It would take us two days to walk all of it,’ says Andrew Juskaitis, Giant’s global product marketing manager. A large components truck trundles past. ‘That is just the Sram one,’ he adds. ‘There are others for other component manufacturers. A company this size requires some appropriately scaled internal logistics solutions.’
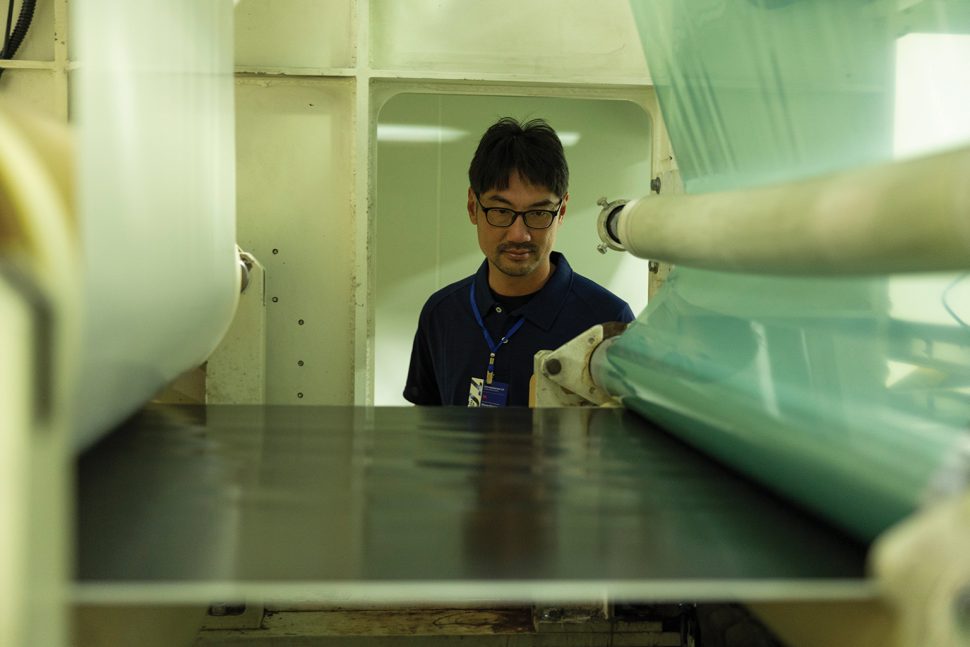
Inside we’re directed to the part of the facility where Giant bikes are born. Dozens of black spools of Japanese Toray carbon are slotted into huge machines, which feed the carbon fibre into another set of machines that gather the threads together and impregnate them with a special resin to form the sheets, known as prepreg, that will be used to create the frames and wheel rims of Giant’s road bikes. If this sounds like par for the course in carbon composite frame construction, it’s far from the case.
Most brands, even the biggest names, buy their carbon already in prepreg form. Giant is exceptionally rare in making its own prepreg, meaning it can construct all its top-end Advanced SL framesets from the base material up.
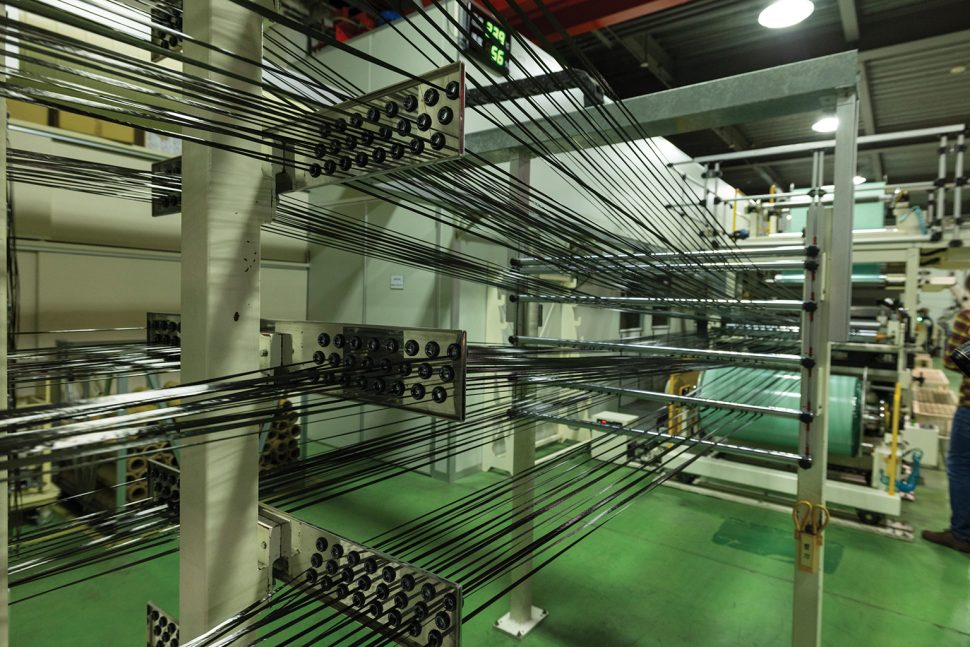
‘By fabricating our own prepreg, we gain complete control over the characteristics of our frames – weight, stiffness, ride quality – because the raw material can be customised. Other brands have to work around set compositions,’ says Juskaitis.
The prepreg looks innocuous when it comes out, like sheets of black tracing paper wound onto large rolls. They are nondescript to the point where you might walk past and not know what they are – not that you would be strolling past, as the rolls are stored in huge industrial freezers that hold anywhere from a 15 to 30-day supply. Given that more than 2,700 bikes leave the factory daily, that’s a lot of carbon.
Fabricating its own prepreg allows Giant to construct composite sheets according to its own recipe. And with over 40 years of knowledge and work with composites, Giant claims to have industry-leading knowledge in honing and refining carbon production. When asked if Giant fabricates prepreg for other brands, Juskaitis says, ‘Yes, to their specifications. Even if we disagree with their recipe.’
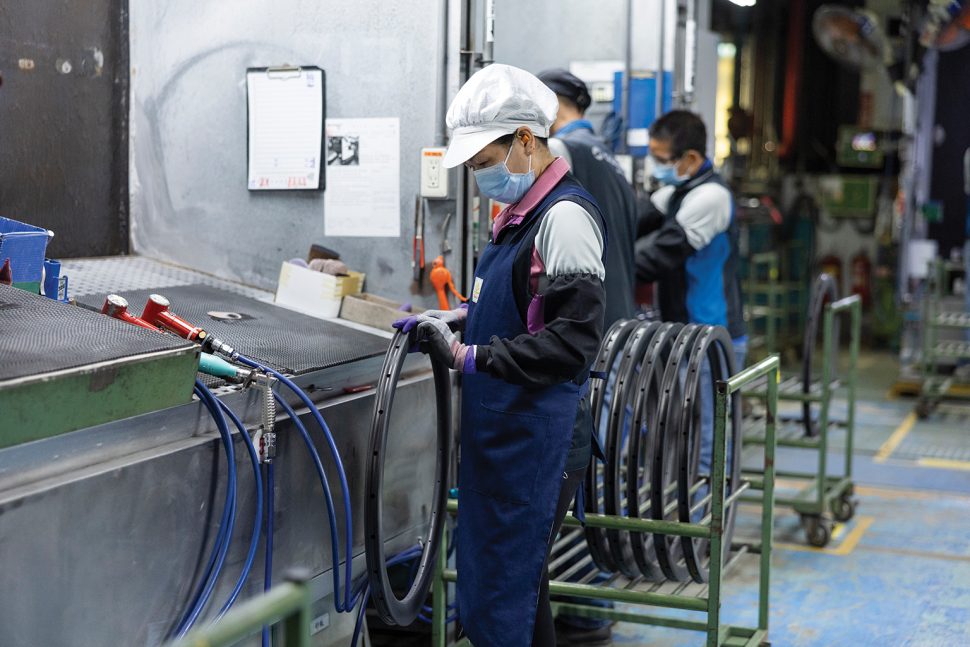
Cutting edge
Cold cut and layup may sound like a Michael Jordan set play, but these are actually the next steps in frame fabrication. Most notable is the cold-blade cutting, Giant’s latest advancement for cutting the composite sheets.
‘Around 97 per cent of all composite swatches are cut using a normal stamping method, which uses a steel die not unlike a cookie cutter,’ says Juskaitis. ‘This produces fairly accurate, high-production pieces. Cold-blade accounts for the other three per cent, such as our Advanced SL applications, where we require smaller, intricate swatches to be laid up with precision.
‘These types of swatches used to be cut using a laser, but we found the high heat of the laser prematurely activated the composite, sometimes resulting in a less-than-acceptable finished piece. Cold-blade cutting is more laborious, taking about four times longer to produce a finished piece, but the end result is better.’
Although a few glimpses of this process have surfaced on YouTube, Giant has otherwise kept a veil of secrecy around this advancement.
‘We don’t know of any other cycling manufacturer that uses this technology,’ Juskaitis says. ‘It has been used strictly in the aerospace sector until the new TCR Advanced SL was developed last year.’
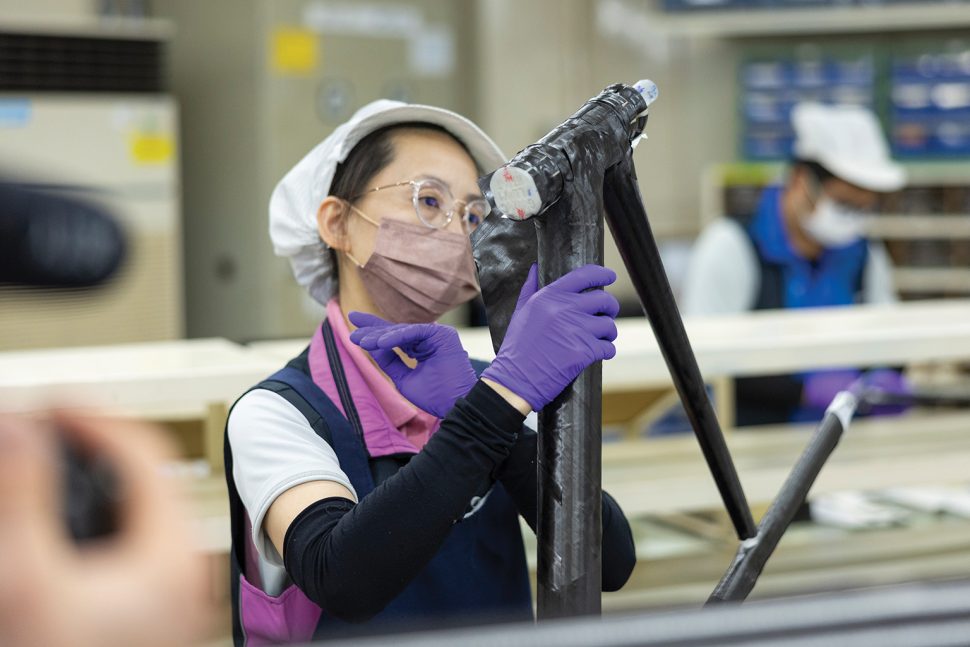
For all the automation in Giant’s industrial manufacturing process, the laying up of carbon in the frame fabrication is a process still only trusted to human hands, and the company’s most experienced ones at that. Frame fabricators must first prove their skills in other carbon layup products, such as wheels, before they are considered for a role in frame fabrication.
Watching the fabricators in action is mesmerising as they meticulously and expertly place each piece of precisely cut carbon fibre prepreg into the mould. Don’t let anyone tell you that modern carbon race bikes are not handmade by artisans.
After curing, facing and finishing, framesets are ready to be painted and assembled but not before each and every fork is X-rayed. Whether it’s branded Giant or being produced for another company, Giant ensures that every part it makes is safety-checked to ensure there are no faults within the carbon construction that might undermine its strength or robustness. It’s not just forks; every carbon rim is also sent through the X-ray and assessed. And then there’s the fatigue testing.
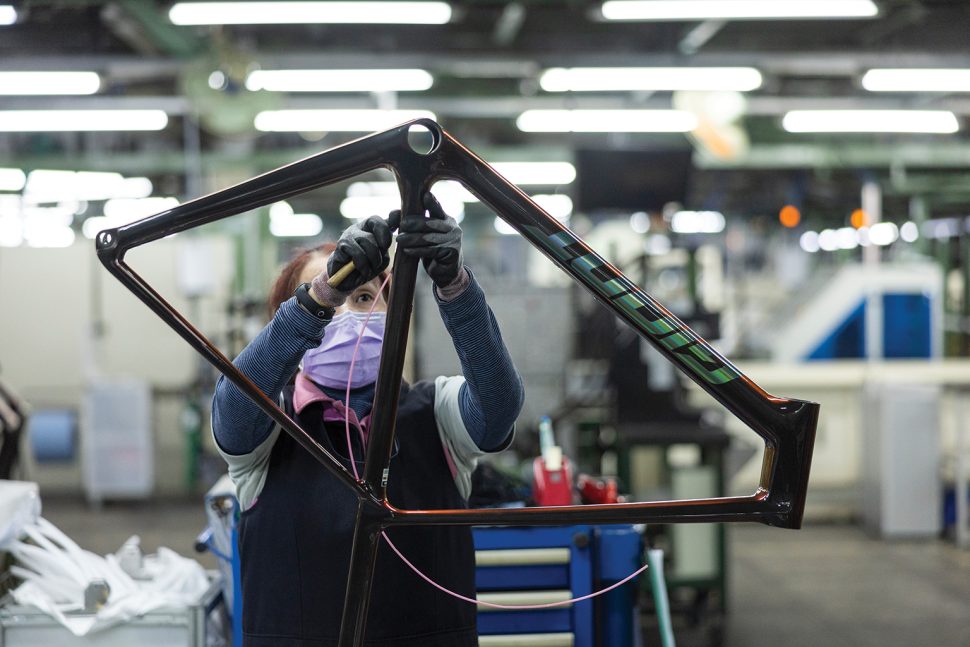
‘Frames are tested to 20 per cent above ISO safety standards at four stages: engineering testing, development testing, pre-production testing and mass production testing,’ says Juskaitis.
The testing room is full of bicycle torture contraptions that bend and twist the poor frames at all kinds of angles. It’s painful to watch but strangely confidence-inspiring.
Painting is also done in-house and is a process where Giant’s proficiency is on the rise. The latest TCR’s Maraya Blue team frameset, as well as the cool Opal colourway, are evidence of this. They’re worlds apart from the basic two-block colour schemes found on framesets as recently as five years ago.
Once dry, the frames roll into the assembly area. Giant’s assembly workforce has the process so dialled, Juskaitis says, that from base frame to essentially rideable bike takes just 15 minutes – about the same time it would take a competent home mechanic to tape the bars. Every hour roughly 114 complete bikes are boxed up and ready to go.
The maker’s maker
Emerging from the assembly area, we snatch a tantalising glimpse of frames bearing the insignias of other major brands. It would be impolite to name those brands here, yet Giant makes no attempt to conceal its work for other suppliers. It is plainly confident enough in its own processes that the bikes it makes for other companies will not reflect poorly on Giant, nor will those other brands be reluctant to reveal where their bikes are produced.

Certainly any bikes made here are going to be of the very top level. Giant Taiwan is the only one of its nine facilities worldwide that produces its Advanced SL-tier models, so cutting-edge tech is the only tech employed at this factory. There’s simply no way Giant could down-spec its production processes enough to create lower-quality competitor frames, meaning the bikes manufactured here for other brands can only be of similarly high quality.
That said, the proportion of bikes Giant makes for other brands is diminishing. ‘Some 70 per cent of production here is for the Giant and Liv brands, which is a shift from even five years ago,’ says Juskaitis.
Despite its enormous size, Giant is still growing. And its attitude towards technology and production processes – creating complete bikes from the carbon threads upwards – means it is growing in quality and prestige at the same time. Soon the phrase ‘it’s made by Giant’ will come to mean something very different.
• This article originally appeared in issue 158 of Cyclist magazine. Click here to subscribe
The post Inside Giant’s Taiwan factory appeared first on Cyclist.